Mantenimiento preventivo: definición, métodos y guía de aplicación para la industria
Resumen
- ¿Qué es el mantenimiento preventivo?
- ¿Por qué adoptar el mantenimiento preventivo en la industria?
- Los tres tipos de mantenimiento preventivo
- ¿Cómo se elabora un plan de mantenimiento preventivo eficaz?
- Mantenimiento preventivo e IoT: hacia la industria conectada
- Nuestras soluciones para digitalizar tu mantenimiento
- ¿Cómo puedes medir la eficacia de tu mantenimiento preventivo?
- FAQ – Preguntas frecuentes sobre el mantenimiento preventivo
- Actúa con FOUR DATA
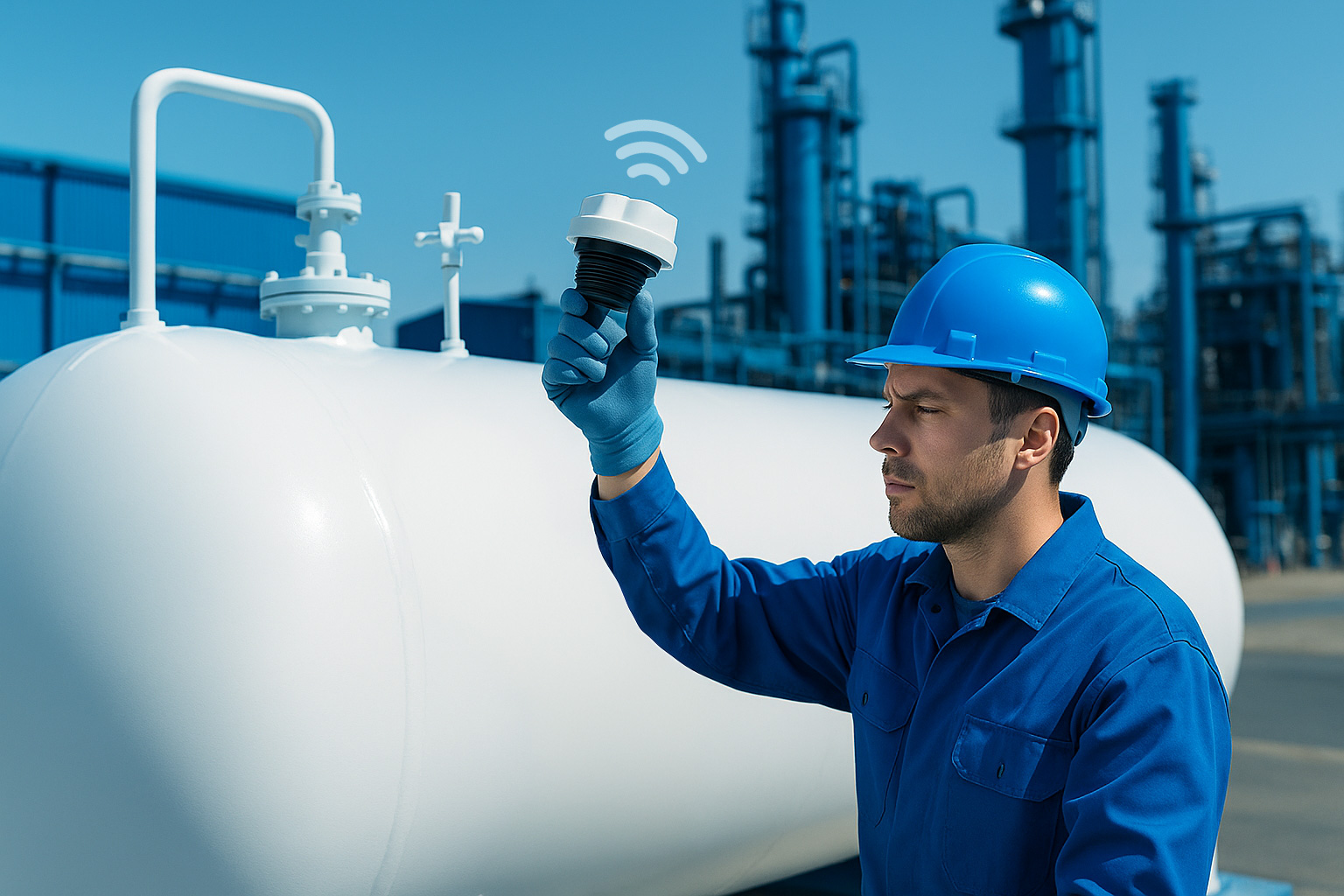
En un mundo industrial cada vez más automatizado, la continuidad de los equipos funcionamiento de los equipos es una cuestión estratégica para cualquier empresa. Las interrupciones de la producción, aunque sean temporales, pueden provocar importantes pérdidas económicas, perjudicar el rendimiento global y aumentar los riesgos para los operadores.
En mantenimiento preventivo es una respuesta eficaz a estos problemas. Al anticipar las averías, prolongar la vida útil de las máquinas y estructurar las intervenciones, permite a los fabricantes reducir sus costes y sus paradas imprevistasy aplicar una gestión técnica racional de gestión.
En esta guía, presentamos los diferentes tipos de tipos de mantenimiento preventivola página los pasos clave para establecer un plan eficazy el valor añadido de una estrategia conectada gracias a las tecnologías IoT. Este contenido está dirigido a responsables de mantenimiento, ingenieros industriales y responsables de la toma de decisiones que quieran optimizar su rendimiento operativo y asegurar sus instalaciones de producción.
¿Qué es el mantenimiento preventivo?
Definición y cuestiones industriales
En mantenimiento preventivo abarca todas las acciones previstas para mantener un equipo equipo en buen funcionamientoy evitar que se produzcan averías antes de que provoquen parada imprevista o deterioro. A diferencia de una intervención curativa, se basa en una estrategia anticipatoria integrada con la gestión de activos industriales.
En un contexto en el que productividadla seguridad y disponibilidad de la máquina son impulsores del rendimiento, el mantenimiento preventivo se está convirtiendo en un pilar esencial. Permite a las empresas limitar riesgo de averíaoptimizar el uso de los medios técnicos técnicos y humanos y humanos, al tiempo que se prolonga la vida útil de piezas críticas piezas críticas.
Integrando el mantenimiento en la fase de diseño y siguiendo un plan estructurado plan estructuradoplan, los fabricantes pueden reducir los costes a largo plazo y mejorar el control de su producción.
🧠 ¿Lo sabías?
➡️ Hasta el 70% de las averías pueden evitarse mediante un mantenimiento preventivo bien estructurado (fuente: estudio AFIM).
¿Cuál es la diferencia entre mantenimiento preventivo y correctivo?
Aquí tienes una tabla comparativa clara para distinguir entre estos dos tipos de mantenimiento, que a menudo se confunden:
Criterios | Mantenimiento preventivo | Mantenimiento correctivo |
---|---|---|
Enfoque | Planificado y anticipado | Reactivo, después del panel |
Objetivo | Prevenir averías | Restablecer el funcionamiento tras una avería |
Coste medio de la intervención | Más bajo (evita daños colaterales) | Más elevado (avería imprevista, emergencia, a veces sustitución total) |
Impacto en la producción | Bajo (paradas programadas, duración optimizada) | Alto (parada repentina, pérdida de producción, penalización del cliente) |
Uso de datos | Sí (análisis del ciclo, estado, sensores, etc.) | Poco o nada (intervención posterior al problema) |
Un ejemplo típico | Sustitución preventiva de una junta | Sustitución de un motor tras un sobrecalentamiento no detectado |
🎯 Puntos a vigilar
No confundir preventivo con predictivo la primera se basa en un calendario o estado observadomientras que la segunda se basa en modelos de datos y algoritmos para predecir una avería.
¿Por qué adoptar el mantenimiento preventivo en la industria?
Reducción de los costes asociados a las averías
En el sector industrial, una interrupción de la producción puede costar varios miles de euros por hora. A avería imprevista a menudo requiere la movilización urgente de recursos internos o externos, lo que conlleva sustitución de piezas en situaciones críticasy a veces puede comprometer los compromisos con el cliente. Por el contrario, una mantenimiento preventivosistemático o condicional, ayuda a controlar estos sucesos y a suavizar su impacto económico.
En intervenciones previstas reducir el coste de compra y almacenamiento de piezas, evitar las horas extraordinarias no planificadas y limitar las pérdidas de explotación. A largo plazo, este planteamiento es en gran medida rentablesobre todo en entornos de alta velocidad o donde se espera un alto nivel de disponibilidad.
💡 Cifras clave
En coste medio de una hora de inactividad de una máquina se estima en entre 2.000 y 5.000 euros en la industria manufacturera (fuente: Deloitte, 2023).
Optimizar la productividad
Adoptar el mantenimiento preventivo significa garantizar una disponibilidad continua equipos críticos. Al reducir paradas intempestivasSe respetan mejor los ciclos de producción y se mejora el rendimiento global de la línea industrial. Este enfoque permite una mejor organización de los recursoscon menos interrupciones y una mejor trazabilidad de las intervenciones.
«Con más de 6.000 depósitos conectados en Francia, necesitábamos una solución de supervisión continua. Gracias a los sensores conectados y a la interfaz Four Data, pudimos anticipar las fluctuaciones de volumen, optimizar nuestras rondas y asegurar nuestra red.»
– Antargaz, cliente de Four Data desde 2002
Una advertencia
“Algunas soluciones no integran de forma nativa la gestión de accesos o la trazabilidad completa”.
Proteger los entornos industriales
El mantenimiento preventivo también es una garantía de seguridad. Identificando y tratando las causas de las averías antes de que se vuelvan críticas, podemos reducir el número de riesgo de accidentesaccidentes rotura de material oincendios eléctricos. Contribuye a un entorno de trabajo más estable que cumple los requisitos normativos.
✅ Reducción de riesgos gracias a las medidas preventivas :
- Accidentes por sobrecalentamiento o fallo mecánico
- Fugas de fluidos o productos peligrosos
- Descargas eléctricas causadas por componentes desgastados
- Mal funcionamiento de los sistemas de seguridad (frenos, válvulas, detectores)
Prolongar la vida útil de los equipos
Equipos bien mantenidos más tiempofunciona más eficazmente y requiere menos sustituciones no programadas. Gracias a un control riguroso deestado de las piezasy los umbrales de desgaste, los fabricantes pueden optimizar el rendimiento de sus equipos retorno de la inversión en equipos.
Tomemos el ejemplo de una bomba industrial: sin mantenimiento, su vida útil puede limitarse a 4 años. Con revisiones periódicas y sustituciones selectivas, puede alcanzar de 7 a 9 años sin pérdida de rendimiento.
📊 Cifras clave (media) :
- +40% más de vida útil para un motor monitorizado por condiciones
- +60% en rodamientos revisados cada 6 meses
- -25% de reducción del consumo de energía con un compresor bien ajustado
🛠️ Consejos de expertos
«Planifica los controles en función de la criticidad y no simplemente en función de su edad. Esta es la un buen equilibrio entre coste y rendimiento..»
Los tres tipos de mantenimiento preventivo
Mantenimiento sistemático
El mantenimiento sistemático se basa en intervenciones planificadas a intervalos regularesindependientemente del estado real del equipo. Esta estrategia se basa en programas de mantenimiento definidos según las recomendaciones de los fabricantes, el historial de uso o las normas internas.
Es especialmente adecuado para piezas sometidas a un desgaste conocido o cíclico. Aunque puede llevar a la sustitución de componentes que aún funcionan, es reduce considerablemente el riesgo de fallos inesperados en equipos críticos.
✅ Ejemplos de acciones sistemáticas:
- Lubricación de un cojinete cada 500 ciclos
- Sustitución preventiva de los filtros hidráulicos cada 3 meses
- Inspección de los cables eléctricos cada 6 meses
- Ajustar los parámetros del motor en una fecha fija
Mantenimiento condicional
El mantenimiento condicional se realiza sólo cuando las señales detectan una desviación o un umbral críticosin esperar a que se produzca una avería. Se basa en análisis del estado real de los equipos mediante sensores conectados que miden en tiempo real parámetros físicos como la temperatura, la vibración, la presión o el caudal.
Este método, posible gracias al IoT industrial, permiteajustar la intervención en el momento adecuadoni demasiado pronto, ni demasiado tarde. Actualmente se utiliza mucho en la industria para optimizar el tiempo de inactividad y reducir costes innecesarios.
🎯 Un ejemplo:
En una cadena de producción alimentaria, un sensor de vibraciones colocado en un motor detecta una variación anormal: ha comenzado el desgaste de los cojinetes. Se genera una alerta a través de la plataforma Four Data. La intervención se planifica antes de la rotura, evitando una parada brusca de la línea.
Mantenimiento predictivo
El mantenimiento predictivo es la forma más avanzada de mantenimiento preventivo. Se basa en análisis estadístico y algorítmico de datos históricos y en tiempo realpara predecir futuros fallos antes de que se produzcan. Este enfoque utiliza modelos de aprendizaje automático ointeligencia artificial para anticipar comportamientos anómalos.
Se basa en grandes volúmenes de datos (big data) recogidos a través del IoT (temperatura, presión, tiempo de ciclo, anomalías, etc.) y permite una estrategia de mantenimiento estrategia de mantenimiento muy específicacon un alto nivel de eficacia.
⚙️ Consejo práctico
Elige el tipo de mantenimiento en función de dos criterios principales:
- El nivel de criticidad del equipo
El coste de la intervención en relación con el riesgo de avería.
👉 A veces, basta con un simple control sistemático; otras veces, sólo una estrategia condicional o predictiva permitirá gestionar con precisión el riesgo industrial.
¿Cómo se elabora un plan de mantenimiento preventivo eficaz?
Evaluación e inventario del equipo
Antes de elaborar un plan de mantenimiento, es esencial hacer un inventario de todos los equipos que hay que mantener. Esta etapa identifica los activos críticos y sienta las bases de una gestión estructurada. La evaluación no se limita a un simple inventario físico: incluye la estado de funcionamiento, l’historial de fallosy criticidad en caso de parada.
Esta fase alimenta directamente la elección de los tipos de intervención (sistemática, condicional, predictiva) y los recursos necesarios que deben asignarse.
📋 Lista de control para cada equipo :
- 📍 Ubicación (zona, línea, sala técnica)
- ⚙️ Estado actual (nuevo, usado, obsoleto)
- 📅 Historial de intervenciones (frecuencia, tipo de fallo)
- 🚨 Criticidad (impacto en la producción, la seguridad, el medio ambiente)
- 🔁 Frecuencia de uso
- 🧩 Compatibilidad con el mantenimiento conectado (IoT, sensores, etc.)
Establecer prioridades y objetivos
Una vez recogidos los datos, tenemos queorganizar las prioridades. No todos los equipos tienen el mismo nivel de riesgo o impacto: un simple compresor auxiliar no presenta los mismos retos que una bomba dosificadora crítica en una línea de producción alimentaria.
El objetivo es dirigir los esfuerzos de mantenimiento allí donde tengan más valor – y alinear los objetivos con las realidades operativas: menos paradas, mayor seguridad, coste total de propiedad (TCO) controlado.
Equipo | Frecuencia de uso | Criticidad (impacto en caso de fallo) | Puntuación de prioridad |
---|---|---|---|
Bomba A | Alto | Alto (parada completa de la línea) | ⭐️⭐️⭐️⭐️ |
Motor B | Medio | Medio (ralentización) | ⭐️⭐️ |
Ventilador C | Bajo | Bajo | ⭐️ |
❗ Un error frecuente
Subestimar los activos secundarios A menudo son la causa de fallos en cascadacomo un sensor olvidado que distorsiona la regulación de un equipo crítico.
Planificación de tareas y recursos
Una vez definidos los objetivos, el siguiente paso eselaborar un calendario claro y realista. Debe tener en cuenta la disponibilidad de equiposde equipos técnicosTambién puede utilizarse en periodos de gran actividad industrial. Lo ideal sería integrarlo en un herramienta GMAO o una plataforma IoTcomo la que ofrece Four Data.
📅 Ejemplos de tareas a planificar:
- Comprobación visual semanal del nivel de aceite
- Sustitución de la correa cada 2 meses
- Comprueba las conexiones de los sensores antes del reinicio estacional
📆 Planificación sugerida :
Gantt simplificado → Tareas por equipo / por mes / por recurso interno/externo
Definición y seguimiento de los indicadores de resultados
Aplicar un plan de mantenimiento sin indicadores de seguimiento es como volar a ciegas. Es esencial medir la eficacia del sistema controlando KPIs indicadores. Estos indicadores permiten ajustar la estrategia, demostrar el retorno de la inversión y detectar a tiempo las desviaciones.
📈 Indicadores clave a controlar :
- MTBF (Tiempo medio entre fallos): tiempo medio entre 2 fallos
- MTTR (Tiempo medio de reparación): tiempo medio de reparación
- Tasa de mantenimiento planificado Relación entre el mantenimiento planificado y el mantenimiento total
- Tasa de disponibilidad de la máquina: porcentaje de tiempo de actividad
Mejora continua de los procesos
Un buen plan de mantenimiento nunca debe permanecer estático. Gracias a la PDCA (Planificar-Hacer-Verificar-Actuar)las empresas pueden mejorar continuamente sus intervenciones. Esto implica analizar periódicamente los datos recogidos, ajustar las frecuencias, añadir sensores o revisar las prioridades en función de los cambios en el entorno industrial.
🔄 Ciclo PDCA aplicado al mantenimiento :
- Planifica Definir acciones basadas en objetivos
- Hacer realizar tareas con un seguimiento riguroso
- Comprueba analizar los indicadores de resultados
- Actúa Ajustar horarios, métodos y herramientas
Esta dinámica coincide plenamente con el rendimiento industrial sobre todo en los centros conectados.
Mantenimiento preventivo e IoT: hacia la industria conectada
Supervisión inteligente con sensores IoT
El mantenimiento preventivo entra en una nueva dimensión cuando se apoya en elIoT industrial. Equipando maquinaria y equipos de sensores inteligenteslas empresas pueden recopilar continuamente datos críticos temperatura, presión, vibración, niveles de fluidos, índices de desgaste, etc.
Estos sensores permiten un seguimiento detallado del estado real de las instalaciones, y activan automáticamente alertas o escenarios de intervención condicional en cuanto se alcanza un umbral crítico está anticuada. Ya no nos contentamos con programar: somos reacciona en el momento adecuadocon precisión.
🔧 Ejemplos de datos recogidos en tiempo real:
- Temperatura del motor hasta 85°C
- Reducción progresiva de la presión en un yacimiento
- Aumento anormal de las vibraciones en una bomba
Análisis de datos en tiempo real
La eficacia del sistema depende de la capacidad de interpretar rápidamente los datos. Gracias a una interfaz de supervisión como la de Four Data, los equipos pueden ver de un vistazo el estado de cada equipo, las alertas actuales y las previsiones de futuras intervenciones.
✅ Ventajas concretas de un salpicadero conectado :
- Visión centralizada de todos los equipos en producción
- Supervisión de umbrales críticos personalizables
- Historial de alertas por máquina
- Priorización automática de las intervenciones
- Exporta informes para análisis o auditoría
Optimización a través de nuestra plataforma Four Data
En Four Data, hemos diseñado una plataforma IoT modular que se adapta a las necesidades de cada centro industrial. Nuestra solución te permite conectar cualquier tipo de equipoindependientemente del sensor o de la red utilizada (Sigfox, NB-IoT, LTE-M, etc.).
🎯 Módulos disponibles en nuestra plataforma:
- 🔌 Conectividad universal (redes públicas o privadas)
- ⚠️ Alertas inteligentes (SMS, correo electrónico, panel de control)
- 📊 Análisis de tendencias (cambios en los parámetros)
- 🧰 Programación del trabajo (integración GMAO)
- 📁 Informes exportables y auditables
📦 Nuestra oferta MCO (Mantenimiento en Condiciones Operativas)
Four Data ofrece un servicio integral para supervisar y optimizar tus activos conectados, que incluye instalación, gestión de alertas, supervisión remota y apoyo a la toma de decisiones. FOUR DATA garantiza la longevidad de tus instalaciones conectadas gracias a un equipo especializado de instaladores de campo. Este servicio ya se utiliza en sectores exigentes como el del petróleo y el gas, sobre todo para el mantenimiento de depósitos.
Nuestras soluciones para digitalizar tu mantenimiento
Software de GMAO e interfaz personalizada
En Four Data, ofrecemos una solución completa para gestión del mantenimiento asistida por ordenador (GMAO)integrada en nuestra solución MESA Y SENS. Esta interfaz se ha diseñado para ofrecer experiencia fluidacon una personalización adaptada a tus usos industriales.
Centraliza toda la información que necesitan tus equipos: estado de los equipos, historial de trabajo, planificación de tareas, alertas condicionales e informes de análisis.
🧰 Características principales de nuestra GMAO integrada :
- 🔧 Supervisión tasa de averías e intervenciones
- 🛠️ Planificación de operaciones de mantenimiento por activo
- 📅 Tiempo de instalación con previsión trimestral
- 📑 Informe de intervención automática
- 📲 Alertas multicanal correo electrónico, SMS, notificaciones de plataforma
- 🖥️ Módulo Autonomía para la configuración local
Nuestra GMAO es una verdadera palanca para agilizar la gestión técnicamejorar la la capacidad de reacción de los equiposy garantizar la trazabilidad de las operaciones.
Integración de sensores, panel de IoT e informes
Gracias a nuestra arquitectura abierta, Four Data puede conectar cualquier tipo de sensor (temperatura, nivel, vibración, etc.) a través de redes como LPWAN, NB-IoT, LTE-M o 4Gpara alimentar tu cuadro de mandos IoT personalizado.
La plataforma recoge, analiza y añade valor a datos técnicos del campo para automatizar la toma de decisiones: envío de alertas, lanzamiento de escenarios de mantenimiento, generación de informes, seguimiento de los índices de funcionamiento y consumo.
🔄 Arquitectura simplificada :
Sensores industriales → Redes IoT → Recogida y alojamiento seguro de datos → Interfaces DESK & SENS
🖥️ Portal de supervisión llave en mano :
- Compatible con Petróleo y gasprocesamiento de alimentos, industria pesada
- Exportar datos para auditorías RGPD
- Infraestructura de SI personalizada, incluido el alojamiento
- Control remoto del consumo o del estado del equipo
🧩 Beneficio clave
Gracias a la digitalización a través de Four Data, nuestros clientes ahorran hasta un 20% de tiempo para detectar detección de anomalías críticasgracias a la establecimiento de escenarios de alerta inteligentes e informes informes automatizados.
📞 ¿Quieres ver nuestra interfaz en acción?
👉 Concierta una cita con uno de nuestros expertos para una demostración personalizada : Contacta con nosotros
¿Cómo puedes medir la eficacia de tu mantenimiento preventivo?
Indicadores clave a controlar (MTBF, MTTR, tasa de disponibilidad)
Aplicar una estrategia de mantenimiento preventivo sólo tiene sentido si se puede evaluada objetivamente. Para conseguirlo, varios indicadores técnicos se utilizan para medir los efectos de las intervenciones en el rendimiento general de los equipos.
He aquí los tres principales KPI que debes controlar:
Indicador | Definición | Fórmula | Objetivo |
---|---|---|---|
MTBF (Tiempo medio entre fallos) | Tiempo medio entre fallos | MTBF = Tiempo total de actividad / Nº de fallos | Ampliar los periodos sin fallos |
MTTR (Tiempo medio de reparación) | Tiempo medio necesario para reparar un equipo | MTTR = Tiempo total de reparación / Nº de intervenciones | Reducir el tiempo de inactividad |
Tasa de disponibilidad | Porcentaje de tiempo que el equipo está operativo | Dispo = MTBF /(MTBF + MTTR) × 100 | Maximizar la utilización de los equipos |
Análisis del ROI y mejora continua
Además de los indicadores técnicos, es esencial evaluar el rendimiento de la inversión (ROI) de mantenimiento preventivo. Este cálculo se utiliza para validar las elecciones realizadas y orientar las futuras decisiones de gestión.
Un ROI positivo significa que el ahorro generado por la reducción de averías, paradas y sustituciones de emergencia compensan la inversión inicial en herramientas, sensores y recursos.
📊 Un ejemplo sencillo:
- Costes evitados (en 12 meses): 45.000 euros (averías, pérdida de producción)
Coste total del plan preventivo (hardware, software, intervención): 28.000 euros
👉 Ganancia neta = 17 000 €
👉 ROI = (45 000 – 28 000) / 28 000 = 60 %
💬 A tener en cuenta
En la mayoría de los casos industriales, el ROI de una estrategia de mantenimiento preventivo digitalizada se hace visible en menos de 6 mesesgracias sobre todo a la reducción de las averías imprevistas y a la optimización de los ciclos de mantenimiento.
FAQ – Preguntas frecuentes sobre el mantenimiento preventivo
Actúa con FOUR DATA
Adoptar un mantenimiento preventivo digitalsignifica dotarse de los medios paraoptimizar la produccióny reducir los costes asociados a los tiempos de inactividad, y paragarantizar el futuro a largo plazo de sus instalaciones. Gracias a nuestra oferta llave en mano y a nuestro servicio MCOayudamos a los fabricantes a una gestión inteligente de sus equiposdesde la instalación hasta la supervisión remota.
👨🔧 Como Antargazque ahora gestiona más de 6.000 depósitos conectados utilizando nuestra tecnología, puedes confiar en una probada plataforma probadadiseñada para responder a tus retos sobre el terreno.
👉 Contacta con nuestros expertos para evaluar tu proyecto o descubrir nuestra interfaz.
📅Concierte una cita con un asesor de Four Data
También te pueden interesar estos artículos :