Maintenance préventive : définition, méthodes et guide d’application en industrie
Résumé
- Qu’est-ce que la maintenance préventive ?
- Pourquoi adopter une maintenance préventive dans l’industrie ?
- Les trois types de maintenance préventive
- Comment établir un plan de maintenance préventive efficace ?
- Maintenance préventive et IoT : vers l’industrie connectée
- Nos solutions pour digitaliser votre maintenance
- Comment mesurer l’efficacité de votre maintenance préventive ?
- FAQ — Les questions fréquentes sur la maintenance préventive
- Passez à l’action avec Four Data
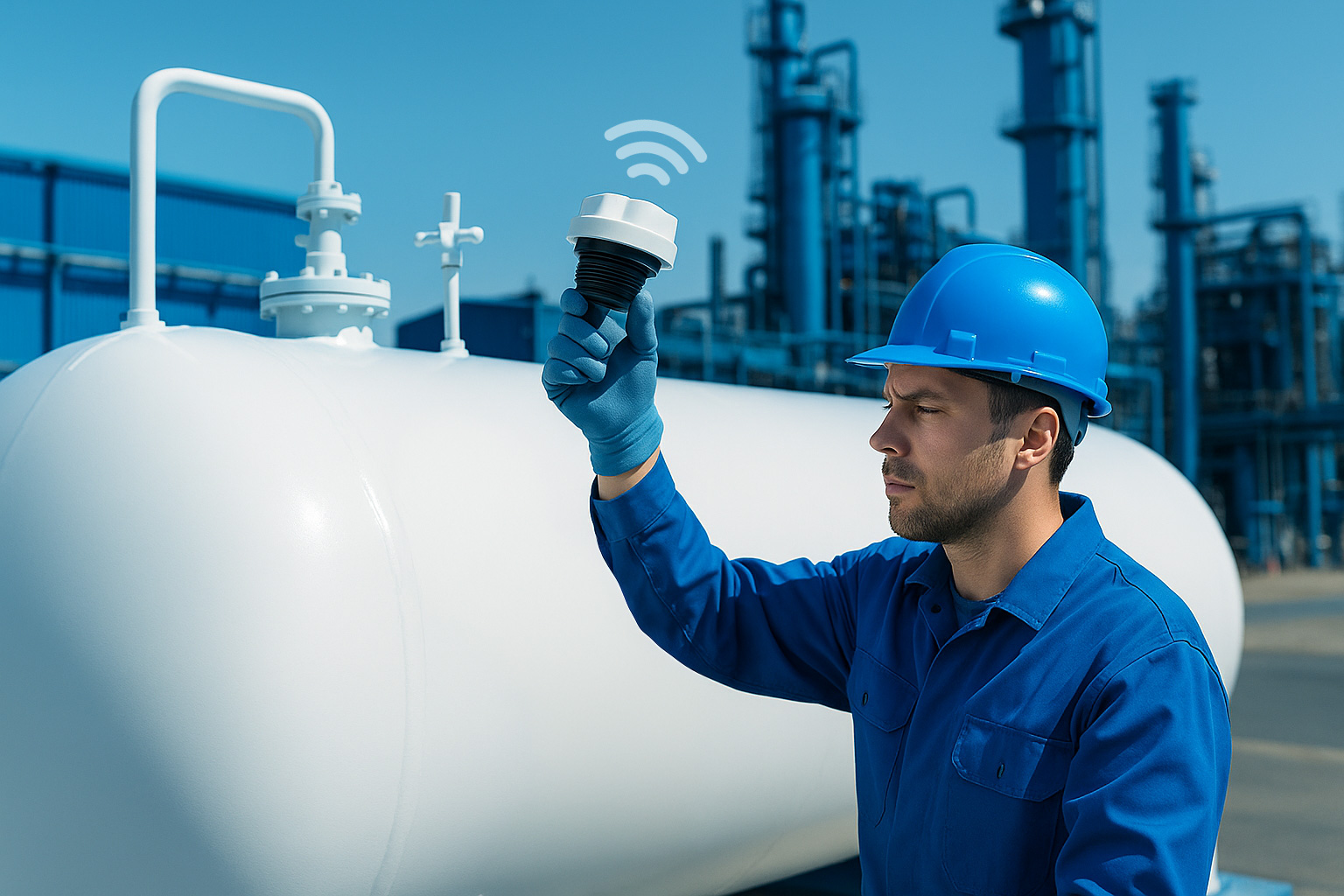
Dans un monde industriel de plus en plus automatisé, la continuité du fonctionnement des équipements est un enjeu stratégique pour toute entreprise. Les interruptions de production, même temporaires, peuvent engendrer des pertes financières conséquentes, altérer la performance globale et accroître les risques pour les opérateurs.
La maintenance préventive s’impose comme une réponse efficace à ces problématiques. En anticipant les pannes, en prolongeant la durée de vie des machines et en structurant les interventions, elle permet aux industriels de réduire leurs coûts, leurs arrêts non planifiés, et de mettre en place une gestion technique rationnelle des actifs.
Dans ce guide, nous vous présentons les différents types de maintenance préventive, les étapes clés pour mettre en place un plan efficace, et la valeur ajoutée d’une stratégie connectée grâce aux technologies IoT. Ce contenu s’adresse aux responsables maintenance, ingénieurs industriels ou décideurs souhaitant optimiser leur performance opérationnelle et sécuriser leur outil de production.
Qu’est-ce que la maintenance préventive ?
Définition et enjeux industriels
La maintenance préventive regroupe l’ensemble des actions planifiées visant à maintenir un équipement en bon état de fonctionnement, et à prévenir l’apparition de défaillances avant qu’elles ne provoquent un arrêt non planifié ou une détérioration. Contrairement à une intervention curative, elle repose sur une stratégie anticipative intégrée à la gestion des actifs industriels.
Dans un contexte où la productivité, la sécurité et la disponibilité des machines sont des leviers de performance, la maintenance préventive devient un pilier incontournable. Elle permet aux entreprises de limiter les risques de panne, d’optimiser l’utilisation des ressources techniques et humaines, tout en prolongeant la durée de vie des pièces critiques.
En intégrant la maintenance dès la phase de conception et en suivant un plan structuré, les industriels réduisent les coûts à long terme et améliorent la maîtrise de leur production.
🧠 Le saviez-vous ?
➡️ Jusqu’à 70 % des pannes peuvent être évitées grâce à une maintenance préventive bien structurée (source : étude AFIM).
Quelle est la différence entre maintenance préventive et corrective ?
Voici un tableau comparatif clair pour distinguer ces deux types de maintenance, souvent confondus :
Critère | Maintenance préventive | Maintenance corrective |
---|---|---|
Approche | Planifiée et anticipée | Réactive, post-panne |
Objectif | Éviter la défaillance | Remettre en état après une panne |
Coût moyen d’intervention | Moins élevé (évite dégâts collatéraux) | Plus élevé (panne imprévue, urgence, parfois remplacement total) |
Impact sur la production | Faible (arrêts programmés, durée optimisée) | Fort (arrêt brutal, perte de rendement, pénalité client) |
Utilisation des données | Oui (analyse des cycles, états, capteurs, etc.) | Peu ou pas (intervention après problème) |
Exemple typique | Changement préventif d’un joint d’étanchéité | Remplacement d’un moteur suite à surchauffe non détectée |
🎯 Point de vigilance
Ne pas confondre préventif avec prédictif : le premier repose sur un calendrier ou un état observé, tandis que le second s’appuie sur des modèles de données et des algorithmes pour prévoir une panne probable.
Pourquoi adopter une maintenance préventive dans l’industrie ?
Réduction des coûts liés aux pannes
Dans le secteur industriel, une interruption de production imprévue peut coûter plusieurs milliers d’euros par heure. Une panne non anticipée mobilise souvent en urgence des ressources internes ou externes, engendre des remplacements de pièces en situation critique, et peut parfois compromettre des engagements clients. À l’inverse, une stratégie de maintenance préventive, systématique ou conditionnelle, permet de maîtriser ces événements et d’en lisser les effets économiques.
Les interventions planifiées réduisent le coût d’achat et de stockage de pièces, évitent les heures supplémentaires non anticipées, et limitent les pertes d’exploitation. Sur le long terme, cette approche est largement rentable, notamment dans les environnements à forte cadence ou à haut niveau de disponibilité attendu.
💡 Chiffre clé
Le coût moyen d’une heure d’arrêt machine est estimé à entre 2 000 et 5 000 € dans l’industrie manufacturière (source : Deloitte, 2023).
Optimisation de la productivité
Adopter une maintenance préventive, c’est garantir la disponibilité continue des équipements critiques. En réduisant les arrêts intempestifs, les cycles de production sont mieux respectés, et les performances globales de la ligne industrielle sont améliorées. Cette approche permet une meilleure organisation des ressources, avec moins d’interruptions et une meilleure traçabilité des interventions.
« Avec plus de 6 000 citernes raccordées en France, nous avions besoin d’une solution de surveillance continue. Grâce aux capteurs connectés et à l’interface Four Data, nous avons pu anticiper les fluctuations de volume, optimiser nos tournées et sécuriser notre réseau. »
— Antargaz, client Four Data depuis 2002
Point de vigilance
“Certaines solutions n’intègrent pas nativement la gestion des accès ou la traçabilité complète.”
Sécurisation des environnements industriels
La maintenance préventive est aussi une garantie de sécurité. En identifiant et en traitant les causes de dysfonctionnement avant qu’elles ne deviennent critiques, on réduit les risques d’accidents, de casse matérielle ou d’incendies électriques. Elle participe à un environnement de travail plus stable, conforme aux exigences réglementaires.
✅ Risques réduits grâce au préventif :
- Accidents dus à la surchauffe ou aux ruptures mécaniques
- Fuites de fluides ou produits dangereux
- Chocs électriques causés par des composants usés
- Mauvais fonctionnement de systèmes de sécurité (freins, vannes, détecteurs)
Allongement de la durée de vie des équipements
Un équipement bien entretenu vit plus longtemps, fonctionne plus efficacement et nécessite moins de remplacements imprévus. Grâce à un suivi rigoureux de l’état des pièces, des cycles de fonctionnement, et des seuils d’usure, les industriels optimisent leur retour sur investissement matériel.
Prenons l’exemple d’une pompe industrielle : sans maintenance, sa durée de vie peut être limitée à 4 ans. Avec des contrôles réguliers et des remplacements ciblés, elle peut atteindre 7 à 9 ans d’utilisation sans baisse de performance.
📊 Chiffres clés (en moyenne) :
- +40 % de durée de vie pour un moteur surveillé en conditionnel
- +60 % sur les roulements entretenus tous les 6 mois
- -25 % de consommation énergétique sur un compresseur bien réglé
🛠️ Conseil d’expert
“Planifiez les contrôles en fonction de la criticité des équipements, et non simplement selon leur ancienneté. C’est la condition d’un bon équilibre entre coût et performance.”
Les trois types de maintenance préventive
Maintenance systématique
La maintenance systématique repose sur une intervention planifiée à intervalles réguliers, indépendamment de l’état réel de l’équipement. Cette stratégie repose sur des plannings de maintenance définis selon des recommandations constructeurs, des historiques d’utilisation ou des normes internes.
Elle est particulièrement adaptée aux pièces soumises à une usure connue ou cyclique. Bien qu’elle puisse conduire à remplacer des composants encore fonctionnels, elle réduit considérablement les risques de défaillance imprévue sur les équipements critiques.
✅ Exemples d’actions systématiques :
- Lubrification d’un roulement tous les 500 cycles
- Remplacement préventif de filtres hydrauliques tous les 3 mois
- Inspection des câbles électriques tous les 6 mois
- Réglage des paramètres moteurs à date fixe
Maintenance conditionnelle
La maintenance conditionnelle intervient uniquement lorsque des signaux détectent une dérive ou un seuil critique, sans attendre la panne. Elle repose sur l’analyse de l’état réel des équipements à l’aide de capteurs connectés qui mesurent en temps réel des paramètres physiques comme la température, les vibrations, la pression ou le débit.
Cette méthode, rendue possible par l’IoT industriel, permet d’ajuster l’intervention au bon moment, ni trop tôt, ni trop tard. Elle est aujourd’hui largement utilisée dans l’industrie pour optimiser les temps d’arrêt et réduire les coûts inutiles.
🎯 Exemple concret :
Sur une chaîne de production alimentaire, un capteur de vibration placé sur un moteur détecte une variation anormale : l’usure du roulement est amorcée. Une alerte est générée via la plateforme Four Data. L’intervention est planifiée avant la casse, évitant un arrêt brutal de la ligne.
Maintenance prédictive
La maintenance prédictive est la forme la plus avancée de maintenance préventive. Elle repose sur l’analyse statistique et algorithmique de données historiques et en temps réel, afin de prédire les défaillances futures avant qu’elles ne surviennent. Cette approche utilise des modèles d’apprentissage automatique (machine learning) ou d’intelligence artificielle pour anticiper les comportements anormaux.
Elle s’appuie sur de grands volumes de données (big data) collectés via l’IoT (température, pression, durée de cycle, anomalies…) et permet une stratégie de maintenance ultra ciblée, avec un taux d’efficacité élevé.
⚙️ Astuce pratique
Choisissez le type de maintenance en fonction de deux critères majeurs :
- Le niveau de criticité de l’équipement
Le coût d’intervention par rapport au risque de panne.
👉 Parfois, un simple contrôle systématique est suffisant ; d’autres fois, seule une stratégie conditionnelle ou prédictive permet de gérer le risque industriel avec précision.
Comment établir un plan de maintenance préventive efficace ?
Évaluation et inventaire des équipements
Avant d’élaborer un plan de maintenance, il est indispensable de recenser l’ensemble des équipements à maintenir. Cette étape permet d’identifier les actifs critiques et de poser les bases d’une gestion structurée. L’évaluation ne se limite pas à un simple inventaire matériel : elle intègre l’état de fonctionnement, l’historique des défaillances, et la criticité en cas d’arrêt.
Cette phase alimente directement le choix des types d’interventions (systématique, conditionnelle, prédictive) et les ressources nécessaires à allouer.
📋 Checklist à relever pour chaque équipement :
- 📍 Emplacement (zone, ligne, local technique)
- ⚙️ État actuel (neuf, usé, obsolète)
- 📅 Historique d’interventions (fréquence, type de panne)
- 🚨 Criticité (impact sur la production, sécurité, environnement)
- 🔁 Fréquence d’utilisation
- 🧩 Compatibilité avec la maintenance connectée (IoT, capteurs, etc.)
Définition des priorités et des objectifs
Une fois les données collectées, il convient d’organiser les priorités. Tous les équipements n’ont pas le même niveau de risque ou d’impact : un simple compresseur auxiliaire ne présente pas les mêmes enjeux qu’une pompe de dosage critique dans une ligne de production alimentaire.
L’objectif ici est de cibler les efforts de maintenance là où ils auront le plus de valeur — et d’aligner les objectifs avec les réalités opérationnelles : réduction des arrêts, sécurité accrue, coût total d’exploitation (TCO) maîtrisé.
Équipement | Fréquence d’usage | Criticité (impact si panne) | Score Priorité |
---|---|---|---|
Pompe A | Élevée | Forte (arrêt complet ligne) | ⭐️⭐️⭐️⭐️ |
Moteur B | Moyenne | Moyenne (ralentissement) | ⭐️⭐️ |
Ventilateur C | Faible | Faible | ⭐️ |
❗ Erreur fréquente
Sous-estimer les actifs secondaires : ils sont souvent à l’origine de défaillances en cascade, comme un capteur oublié qui fausse la régulation d’un équipement critique.
Planification des tâches et ressources
Une fois les objectifs définis, la prochaine étape est d’établir un planning clair et réaliste. Il doit tenir compte de la disponibilité des équipements, des équipes techniques, mais aussi des périodes de forte activité industrielle. L’idéal est de l’intégrer dans un outil GMAO ou une plateforme IoT, comme celle que propose Four Data.
📅 Exemples de tâches à planifier :
- Contrôle visuel hebdomadaire de niveau d’huile
- Remplacement de courroie tous les 2 mois
- Vérification connectique capteur avant redémarrage saisonnier
📆 Planning-type suggéré :
Gantt simplifié → Tâches par équipement / par mois / par ressource interne/externe
Définition et suivi des indicateurs de performance
Mettre en place un plan de maintenance sans suivi d’indicateurs revient à piloter à l’aveugle. Il est essentiel de mesurer l’efficacité du dispositif en suivant des KPIs adaptés. Ces indicateurs permettent d’ajuster la stratégie, de démontrer le ROI et de détecter les dérives à temps.
📈 Indicateurs clés à suivre :
- MTBF (Mean Time Between Failures) : durée moyenne entre 2 pannes
- MTTR (Mean Time To Repair) : durée moyenne de réparation
- Taux de maintenance planifiée : ratio interventions planifiées / totales
- Taux de disponibilité machine : pourcentage de temps de fonctionnement
Amélioration continue du processus
Un bon plan de maintenance ne doit jamais rester figé. Grâce au cycle PDCA (Plan-Do-Check-Act), les entreprises peuvent améliorer en continu leurs interventions. Cela passe par l’analyse régulière des données collectées, l’ajustement des fréquences, l’ajout de capteurs ou la révision des priorités en fonction de l’évolution de l’environnement industriel.
🔄 Cycle PDCA appliqué à la maintenance :
- Plan : définir les actions en fonction des objectifs
- Do : exécuter les tâches avec suivi rigoureux
- Check : analyser les indicateurs de performance
- Act : ajuster les plannings, méthodes et outils
Cette dynamique s’inscrit pleinement dans les démarches de performance industrielle continue, notamment dans les sites connectés.
Maintenance préventive et IoT : vers l’industrie connectée
Surveillance intelligente avec des capteurs IoT
La maintenance préventive entre dans une nouvelle dimension lorsqu’elle s’appuie sur l’IoT industriel. En équipant les machines et équipements de capteurs intelligents, les entreprises peuvent collecter en continu des données critiques : température, pression, vibration, niveau de liquide, taux d’usure…
Ces capteurs permettent une surveillance fine de l’état réel des installations, et déclenchent automatiquement des alertes ou des scénarios d’intervention conditionnelle dès qu’un seuil critique est dépassé. On ne se contente plus de programmer : on réagit au bon moment, avec précision.
🔧 Exemples de données collectées en temps réel :
- Température d’un moteur atteignant 85 °C
- Diminution progressive de pression dans un réservoir
- Augmentation anormale de vibration sur une pompe
Analyse des données en temps réel
L’efficacité du dispositif repose sur la capacité à interpréter rapidement les données. Grâce à une interface de supervision comme celle de Four Data, les équipes peuvent consulter, en un coup d’œil, l’état de chaque équipement, les alertes en cours, et les prévisions d’interventions à venir.
✅ Bénéfices concrets d’un dashboard connecté :
- Vue centralisée de tous les équipements en production
- Suivi des seuils critiques personnalisables
- Historique des alertes par machine
- Priorisation automatique des interventions
- Export de rapports pour analyse ou audit
Optimisation via notre plateforme Four Data
Chez Four Data, nous avons conçu une plateforme IoT modulaire qui s’adapte aux besoins de chaque site industriel. Notre solution permet de connecter n’importe quel type d’équipement, quel que soit le capteur ou le réseau utilisé (Sigfox, NB-IoT, LTE-M…).
🎯 Modules proposés sur notre plateforme :
- 🔌 Connectivité universelle (réseaux publics ou privés)
- ⚠️ Alerting intelligent (SMS, mail, tableau de bord)
- 📊 Analyse des tendances (évolution des paramètres)
- 🧰 Planification des interventions (intégration GMAO)
- 📁 Rapports exportables et auditables
📦 Notre offre MCO (Maintien en Condition Opérationnelle)
Four Data propose un service complet de suivi et d’optimisation de vos actifs connectés, incluant l’installation, la gestion des alertes, la supervision à distance et l’accompagnement à la décision. FOUR DATA assure la pérennité de vos installations connectées grâce à une équipe d’installateurs terrain dédiée. Ce service est déjà utilisé dans des secteurs exigeants comme l’Oil & Gas, notamment pour la maintenance de dépôts.
Nos solutions pour digitaliser votre maintenance
Logiciels de GMAO et interface personnalisée
Chez Four Data, nous proposons une solution complète de gestion de maintenance assistée par ordinateur (GMAO), intégrée dans notre portail DESK & SENS. Cette interface a été conçue pour offrir une expérience fluide, avec une personnalisation adaptée à vos usages industriels.
Elle centralise toutes les informations utiles à vos équipes : état des équipements, historique des interventions, planification des tâches, alertes conditionnelles, et rapports d’analyse.
🧰 Fonctionnalités clés de notre GMAO intégrée :
- 🔧 Suivi du taux de panne et des interventions
- 🛠️ Planification des opérations de maintenance par actif
- 📅 Délai d’installation avec prévisionnel trimestriel
- 📑 Rapport d’intervention automatique
- 📲 Alerting multicanal : emails, SMS, notifications plateforme
- 🖥️ Module Autonomie pour paramétrage local
Notre GMAO est un véritable levier pour rationaliser la gestion technique, améliorer la réactivité des équipes, et garantir une traçabilité complète des opérations.
Intégration de capteurs, tableau de bord IoT et reporting
Grâce à notre architecture ouverte, Four Data permet de connecter tout type de capteur (température, niveau, vibration…) via des réseaux LPWAN, NB-IoT, LTE-M ou 4G, pour alimenter en temps réel votre tableau de bord IoT personnalisé.
La plateforme collecte, analyse et valorise les données techniques remontées par le terrain pour automatiser la prise de décision : envoi d’alertes, lancement de scénarios de maintenance, génération de rapports, suivi du taux d’exploitation ou de consommation.
🔄 Architecture simplifiée :
Capteurs industriels → Réseaux IoT → Collecte & hébergement sécurisé → Interface DESK & SENS
🖥️ Portail de supervision clé en main :
- Compatible avec les déploiements Oil & Gas, agroalimentaire, industrie lourde
- Export de données pour audits RGPD
- Infrastructure SI adaptée avec hébergement inclus
- Suivi de consommation ou d’état matériel à distance
🧩 Avantage clé
Avec la digitalisation via Four Data, nos clients gagnent jusqu’à 20 % de temps sur la détection des anomalies critiques, grâce à la mise en place de scénarios d’alerte intelligents et de rapports automatisés.
📞 Vous souhaitez voir notre interface en action ?
👉 Prenez rendez-vous avec un de nos experts pour une démonstration personnalisée : Contactez-nous
Comment mesurer l’efficacité de votre maintenance préventive ?
Indicateurs clés à suivre (MTBF, MTTR, taux de disponibilité)
Mettre en œuvre une stratégie de maintenance préventive n’a de sens que si elle peut être évaluée objectivement. Pour cela, plusieurs indicateurs techniques permettent de mesurer les effets des interventions sur la performance globale des équipements.
Voici les trois principaux KPIs à suivre :
Indicateur | Définition | Formule | Objectif |
---|---|---|---|
MTBF (Mean Time Between Failures) | Temps moyen de fonctionnement sans panne | MTBF = Temps total de fonctionnement / Nb de pannes | Allonger les périodes sans défaillance |
MTTR (Mean Time To Repair) | Durée moyenne nécessaire pour réparer un équipement | MTTR = Temps total de réparation / Nb d’interventions | Réduire le temps d’immobilisation |
Taux de disponibilité | Pourcentage du temps où l’équipement est opérationnel | Dispo = MTBF / (MTBF + MTTR) × 100 | Maximiser l’exploitation des équipements |
Analyse du ROI et amélioration continue
Au-delà des indicateurs techniques, il est essentiel d’évaluer le retour sur investissement (ROI) de la maintenance préventive. Ce calcul permet de valider les choix effectués et d’orienter les futures décisions de gestion.
Un ROI positif indique que les économies générées par la réduction des pannes, des arrêts et des remplacements d’urgence surpassent l’investissement initial dans les outils, les capteurs et les ressources.
📊 Exemple simple :
- Coûts évités (sur 12 mois) : 45 000 € (pannes, perte de production)
Coût total du plan préventif (matériel, logiciel, intervention) : 28 000 €
👉 Gain net = 17 000 €
👉 ROI = (45 000 – 28 000) / 28 000 = 60 %
💬 À noter
Dans la majorité des cas industriels, le ROI d’une stratégie de maintenance préventive digitalisée devient visible en moins de 6 mois, notamment grâce à la réduction des défaillances imprévues et à l’optimisation des cycles de maintenance.
FAQ — Les questions fréquentes sur la maintenance préventive
Passez à l’action avec Four Data
Adopter une stratégie de maintenance préventive digitalisée, c’est se donner les moyens d’optimiser sa production, de réduire les coûts liés aux arrêts, et d’assurer la pérennité de ses installations. Grâce à notre offre clé en main et notre service MCO, nous accompagnons les industriels dans le pilotage intelligent de leurs équipements, de l’installation à la supervision à distance.
👨🔧 Comme Antargaz, qui gère aujourd’hui plus de 6 000 citernes connectées grâce à notre technologie, vous pouvez vous appuyer sur une plateforme éprouvée, pensée pour vos enjeux terrain.
👉 Contactez nos experts pour évaluer votre projet ou découvrir notre interface.
📅 Prendre RDV avec un consultant Four Data
Ces articles peuvent également vous intéresser :