Preventive maintenance: definition, methods and industrial application guide
Summary
- What is preventive maintenance?
- Why adopt preventive maintenance in industry?
- The three types of preventive maintenance
- How do you set up an effective preventive maintenance plan?
- Preventive maintenance and IoT: towards connected industry
- Our solutions for digitizing your maintenance
- How can you measure the effectiveness of your preventive maintenance?
- FAQ – Frequently asked questions about preventive maintenance
- Take action with Four Data
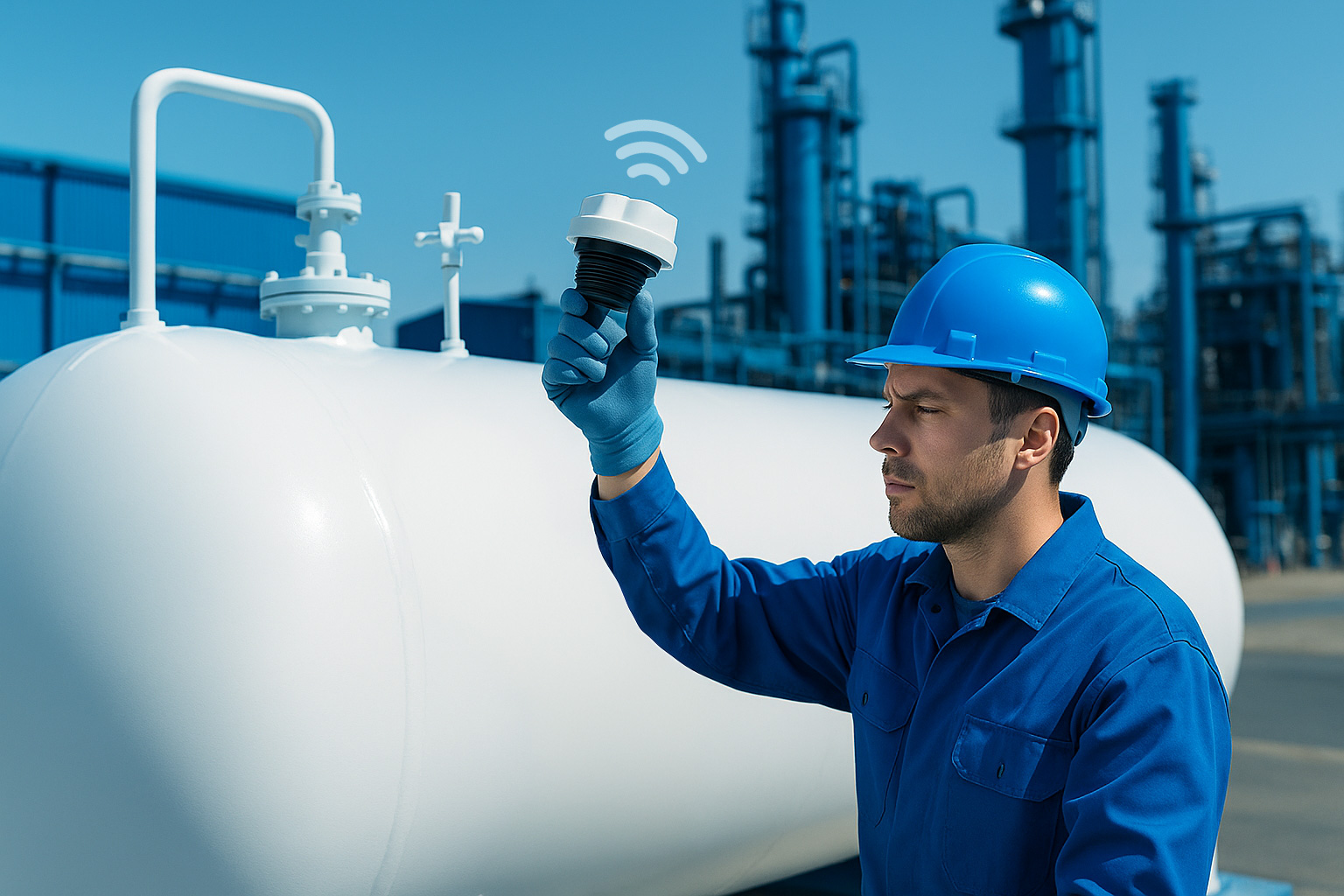
In an increasingly automated industrial world, the continuity of operation of equipment is a strategic issue for any company. Production interruptions, even temporary ones, can lead to substantial financial losses, impair overall performance and increase risks for operators.
Visit preventive maintenance is an effective response to these problems. By anticipating breakdowns, extending machine life and structuring interventions, it enables manufacturers to cut costs, reduce unplanned downtimeand implement rational rational technical management management.
In this guide, we present the different types of types of preventive maintenancethe key steps to setting up an effective planand the added value of a connected strategy thanks to IoT technologies. This content is aimed at maintenance managers, industrial engineers or decision-makers wishing to optimize their operational performance and secure their production facilities.
What is preventive maintenance?
Definition and industrial challenges
Visit preventive maintenance covers all planned actions aimed at maintaining a piece of equipment in good good working orderand prevent the occurrence of failures before they cause an unplanned shutdown or deterioration. Unlike a curative intervention, it is based on a specific anticipatory strategy integrated with industrial asset management.
In a context where productivitythe safety and machine availability are performance drivers, preventive maintenance has become an essential pillar. It enables companies to limit risks of breakdownoptimize the use of technical technical and human and human resources, while extending the service life of critical critical parts.
By integrating maintenance into the design phase and following a structured structured planplan, manufacturers reduce long-term costs and improve control of their production.
🧠 Did you know?
➡️ Up to 70% of breakdowns can be avoided through well-structured preventive maintenance (source: AFIM study).
What’s the difference between preventive and corrective maintenance?
Here is a clear comparison table to help you distinguish between these two types of maintenance, which are often confused:
Criteria | Preventive maintenance | Corrective maintenance |
---|---|---|
Approach | Planned and anticipated | Reactive, post-panel |
Objective | Prevent failure | Recondition after failure |
Average intervention cost | Lower (avoids collateral damage) | Higher (unforeseen breakdown, emergency, sometimes total replacement) |
Impact on production | Low (programmed shutdowns, optimized duration) | High (sudden shutdown, loss of yield, customer penalty) |
Data utilization | Yes (cycle analysis, status, sensors, etc.) | Little or no (post-problem intervention) |
Typical example | Preventive replacement of a seal | Replacement of a motor following undetected overheating |
🎯 Point of vigilance
Do not confuse preventive with predictive the former is based on an observed schedule or observed statewhile the latter is based on data models data models and algorithms to predict a probable failure.
Why adopt preventive maintenance in industry?
Reduce costs related to breakdowns
In the industrial sector, an production interruption can cost several thousand euros per hour. A unanticipated breakdown often mobilizes internal or external resources on an emergency basis, leading to parts replacement in critical situationsand can sometimes compromise customer commitments. Conversely, a preventive maintenancesystematic or conditional, helps to control these events and smooth out their economic impact.
The planned interventions reduce the cost of purchasing and stocking parts, avoid unplanned overtime, and limit operating losses. In the long term, this approach is largely cost-effectiveparticularly in high-speed environments or where high availability is expected.
💡 Key figures
The average cost of one hour of machine downtime is estimated at between €2,000 and €5,000 in the manufacturing industry (source: Deloitte, 2023).
Optimizing productivity
Adopting preventive maintenance means guaranteeing continuous continuous availability critical equipment. By reducing untimely stopsProduction cycles are better respected, and the overall performance of the industrial line is improved. This approach enables better organization of resourceswith fewer interruptions and better traceability of interventions.
“With over 6,000 tanks connected in France, we needed a continuous monitoring solution. Thanks to the connected sensors and Four Data interface, we were able to anticipate volume fluctuations, optimize our rounds and secure our network.”
– Antargaz, a Four Data customer since 2002
Point of caution
“Some solutions don’t natively integrate access management or full traceability.”
Securing industrial environments
Preventive maintenance is also a guarantee of safety. By identifying and treating the causes of malfunctions before they become critical, we reduce the number of risk of accidentsaccidents material breakage orelectrical fires. It contributes to a more stable working environment, in line with regulatory requirements.
✅ Preventive measures reduce risk:
- Accidents due to overheating or mechanical failure
- Fluid or hazardous product leaks
- Electrical shocks caused by worn components
- Malfunction of safety systems (brakes, valves, sensors)
Extending equipment service life
Well-maintained equipment longeroperates more efficiently and requires fewer unscheduled replacements. Thanks to rigorous monitoring ofparts statusand wear thresholds, manufacturers can optimize their return on equipment return on equipment investment.
Take the example of an industrial pump: without maintenance, its service life can be limited to 4 years. With regular checks and targeted replacements, it can reach 7 to 9 years with no loss of performance.
📊 Key figures (average) :
- +40% longer life for condition-monitored motors
- +60% on bearings serviced every 6 months
- 25% less energy consumption with a well-tuned compressor
🛠️ Expert advice
“Plan controls according to criticality equipment, and not simply according to its age. This is the the right balance between cost and performance..”
The three types of preventive maintenance
Systematic maintenance
Systematic maintenance is based on planned intervention at regular intervalsregardless of the actual condition of the equipment. This strategy is based on maintenance schedules defined according to manufacturers’ recommendations, usage histories or internal standards.
It is particularly well suited to parts subject to known or cyclical wear. Although it may lead to the replacement of components that are still functional, it can also be used for considerably reduces the risk of unexpected failure on critical equipment.
✅ Examples of systematic actions:
- Lubrication of one bearing every 500 cycles
- Preventive replacement of hydraulic filters every 3 months
- Inspection of electrical cables every 6 months
- Setting motor parameters on a fixed date
Conditional maintenance
Conditional maintenance intervenes only when signals detect a drift or a critical thresholdwithout waiting for a breakdown. It is based on analysis of actual equipment of equipment using connected sensors which measure physical parameters such as temperature, vibration, pressure or flow in real time.
This method, made possible by industrial IoT, makes it possible tothe right intervention at the right timenot too early, not too late. It is now widely used in industry to optimize downtime and reduce unnecessary costs.
🎯 Case in point:
On a food production line, a vibration sensor placed on a motor detects an abnormal variation: bearing wear has begun. An alert is generated via the Four Data platform. Intervention is planned before the breakage occurs, thus avoiding a sudden shutdown of the line.
Predictive maintenance
Predictive maintenance is the most advanced form of preventive maintenance. It is based on statistical and algorithmic analysis of historical and real-time datato predict future failures before they occur. This approach uses machine learning models orartificial intelligence to anticipate abnormal behavior.
It is based on large volumes of data (big data) collected via the IoT (temperature, pressure, cycle time, anomalies, etc.) and enables an ultra-targeted highly targeted maintenance strategywith a high level of efficiency.
⚙️ Practical tip
Select type of maintenance based on two major criteria:
- The criticality level of the equipment
The cost of intervention in relation to the risk of breakdown.
👉 Sometimes, a simple systematic control is sufficient; other times, only a conditional or predictive strategy can be used to manage industrial risk accurately. industrial risk management.
How do you set up an effective preventive maintenance plan?
Equipment assessment and inventory
Before drawing up a maintenance plan, it is essential to identify all equipment to be maintained. This stage identifies critical assets and lays the foundations for structured management. Valuation is not limited to a simple physical inventory: it includes the operating condition, l’failure historyand criticality in the event of shutdown.
This phase feeds directly into the choice of types of intervention (systematic, conditional, predictive) and the necessary resources to be allocated.
📋 Checklist for each piece of equipment :
- 📍 Location (area, line, equipment room)
- ⚙️ Current condition (new, used, obsolete)
- 📅 Service history (frequency, type of failure)
- 🚨 Criticality (impact on production, safety, environment)
- 🔁 Frequency of use
- 🧩 Compatibility with connected maintenance (IoT, sensors, etc.)
Setting priorities and objectives
Once the data has been collected, we need toorganize priorities. Not all equipment has the same level of risk or impact: a simple auxiliary compressor does not present the same challenges as a critical dosing pump in a food production line.
The aim here is to target maintenance efforts where they will have the most value – and align objectives with operational realities: reduced downtime, improved safety, controlled total cost of ownership (TCO).
Equipment | Frequency of use | Criticality (impact if failure) | Score Priority |
---|---|---|---|
Pump A | High | High (complete line stop) | ⭐️⭐️⭐️⭐️ |
Engine B | Medium | Medium (slowdown) | ⭐️⭐️ |
Fan C | Low | Low | ⭐️ |
❗ Common mistake
Underestimating secondary assets secondary assets: they are often the source of cascading failuressuch as a forgotten sensor that distorts the regulation of critical equipment.
Task and resource planning
Once the objectives have been defined, the next step is todraw up a clear, realistic schedule. It must take into account the equipment availabilityof technical teamsbut also periods of high industrial activity. Ideally, it should be integrated into a CMMS tool or IoT platformplatform, such as that offered by Four Data.
📅 Examples of tasks to be planned :
- Weekly visual oil level check
- Belt replacement every 2 months
- Sensor connection check before seasonal restart
📆 Suggested planning type :
Simplified Gantt → Tasks by equipment / by month / by internal/external resource
Defining and monitoring performance indicators
Implement a maintenance plan without tracking indicators amounts to blind piloting. It is essential to measure the effectiveness of the system by monitoring KPIs indicators. These indicators can be used to adjust strategy, demonstrate ROI and detect drift in good time.
📈 Key indicators to monitor :
- MTBF (Mean Time Between Failures): average time between 2 failures
- MTTR (Mean Time To Repair): average repair time
- Planned maintenance rate ratio of planned to total maintenance
- Machine availability rate: percentage of uptime
Continuous process improvement
A good maintenance plan never has to stand still. Thanks to the PDCA (Plan-Do-Check-Act)companies can continuously improve their interventions. This means regularly analyzing the data collected, adjusting frequencies, adding sensors or revising priorities according to changes in the industrial environment.
🔄 PDCA cycle applied to maintenance :
- Plan Define actions according to objectives
- Do perform tasks with rigorous follow-up
- Check Analyze performance indicators
- Act Adjust schedules, methods and tools
This dynamic is fully in line with the Group’s industrial industrial performance particularly in connected sites.
Preventive maintenance and IoT: towards connected industry
Intelligent monitoring with IoT sensors
Preventive maintenance enters a new dimension when it relies on theindustrial IoT. By equipping machines and equipment from intelligent sensorscompanies can continuously collect critical critical data temperature, pressure, vibration, liquid level, wear rate…
These sensors enable monitoring of the actual state and automatically trigger alerts or conditional intervention scenarios as soon as a critical critical threshold is outdated. We’re no longer content to simply program. reacts at the right momentwith precision.
🔧 Examples of data collected in real time :
- Motor temperature up to 85°C
- Gradual pressure reduction in a reservoir
- Abnormal increase in pump vibration
Real-time data analysis
The effectiveness of the system depends on ability to quickly interpret data. Thanks to a supervision interface like Four Data’s, teams can consult, at a glance, the status of each piece of equipment, current alerts, and forecasts of future interventions.
✅ Concrete benefits of a connected dashboard :
- Centralized view of all equipment in production
- Customizable critical threshold monitoring
- Alert history by machine
- Automatic prioritization of interventions
- Export reports for analysis or audit
Optimization via our Four Data platform
At Four Data, we have designed a modular IoT platform that adapts to the needs of each industrial site. Our solution enables you to connect any type of equipmentregardless of the sensor or network used (Sigfox, NB-IoT, LTE-M…).
🎯 Modules available on our platform :
- 🔌 Universal connectivity (public or private networks)
- ⚠️ Intelligent alerting (SMS, e-mail, dashboard)
- 📊 Trend analysis (evolution of parameters)
- 🧰 Work scheduling (CMMS integration)
- 📁 Exportable and auditable reports
📦 Our MCO (Maintenance in Operational Condition) offer
Four Data offers a complete service for monitoring and optimizing your connected assets, including installation, alert management, remote supervision and decision support. FOUR DATA ensures the longevity of your connected installations thanks to a dedicated team of field installers. This service is already used in demanding sectors such as Oil & Gas, notably for depot maintenance.
Our solutions for digitizing your maintenance
CMMS software and customized interface
At Four Data, we offer a complete solution for computer-aided maintenance management (CMMS) solutionsolution, integrated into our DESK & SENS. This interface has been designed to offer fluid experiencewith customization adapted to your industrial uses.
It centralizes all the information your teams need: equipment status, service history, task planning, conditional alerts and analysis reports.
🧰 Key features of our integrated CMMS :
- 🔧 Monitoring breakdown rate and interventions
- 🛠️ Maintenance maintenance operations by asset
- 📅 Installation lead time with quarterly forecast
- 📑 Automatic intervention report
- 📲 Multi-channel alerting e-mail, SMS, platform notifications
- 🖥️ Module Autonomy for local settings
Our CMMS is a real lever for rationalize technical managementimprove team responsivenessand guarantee complete traceability of operations.
Sensor integration, IoT dashboard and reporting
Thanks to our open architecture, Four Data can connect any type of sensor (temperature, level, vibration, etc.) via LPWAN, NB-IoT, LTE-M or 4G networksnetworks, to feed your customized IoT dashboard.
The platform collects, analyses and adds value to technical data from the field to automate decision-making: sending alerts, launching maintenance scenarios, generating reports, monitoring operating or consumption rates.
🔄 Simplified architecture :
Industrial sensors → IoT networks → Secure data collection & hosting → DESK & SENS interfaces
🖥️ Turnkey supervision portal :
- Compatible with Oil & Gasfood processing, heavy industry
- Data export for RGPD audits
- Customized IS infrastructure including hosting
- Remote monitoring of consumption or equipment status
🧩 Key benefits
With digitalization via Four Data, our customers save up to 20% time on detection of critical anomaliesthanks to the setting up intelligent alert scenarios and automated automated reports.
📞 Would you like to see our interface in action?
👉 Make an appointment with one of our experts for a personalized demonstration : Contact us
How can you measure the effectiveness of your preventive maintenance?
Key indicators to monitor (MTBF, MTTR, availability rate)
Implementing a preventive maintenance strategy only makes sense if it can be objectively assessed. To achieve this, several technical indicators are used to measure the effects of interventions on the overall performance of equipment.
Here are the three main KPIs to track:
Indicator | Definition | Formula | Target |
---|---|---|---|
MTBF (Mean Time Between Failures) | Mean time between failures | MTBF = Total uptime / No. of failures | Extend failure-free periods |
MTTR (Mean Time To Repair) | Average time required to repair a piece of equipment | MTTR = Total repair time / No. of interventions | Reduce downtime |
Uptime rate | Percentage of time equipment is operational | Dispo = MTBF /(MTBF + MTTR) × 100 | Maximize equipment utilization |
ROI analysis and continuous improvement
Beyond technical indicators, it’s essential to evaluate the return on investment (ROI) of preventive maintenance. This calculation helps validate the choices made and guide future management decisions.
A positive ROI indicates that savings generated by the reduction in breakdowns, downtime and emergency replacements outweigh the initial investment in tools, sensors and resources.
📊 A simple example:
- Avoided costs (over 12 months): €45,000 (breakdowns, loss of production)
Total cost of preventive plan (hardware, software, intervention): €28,000
👉 Net gain = 17 000 €
👉 ROI = (45 000 – 28 000) / 28 000 = 60 %
💬 Please note
In most industrial cases, the ROI of a digitalized preventive maintenance strategy becomes visible in less than 6 monthsthanks in particular to the reduction in unforeseen failures and the optimization of maintenance cycles.
FAQ – Frequently asked questions about preventive maintenance
Take action with Four Data
Adopt a digitalized digitalized preventive maintenancemeans giving yourself the means tooptimize productionoptimize reduce costs related to downtime, andand ensure the longevity of your facilities. Thanks to our turnkey offer and service MCOwe support manufacturers in the intelligent control of their equipmentfrom installation to remote supervision.
👨🔧 Like Antargazwhich now manages more than 6,000 connected tanks thanks to our technology, you can rely on a proven proven platformdesigned to meet your challenges in the field.
👉 Contact our experts to evaluate your project or discover our interface.
📅 Make an appointment with a Four Data consultant
You may also be interested in these articles :