Predictive maintenance: definition, benefits and implementation in Industry 4.0
Summary
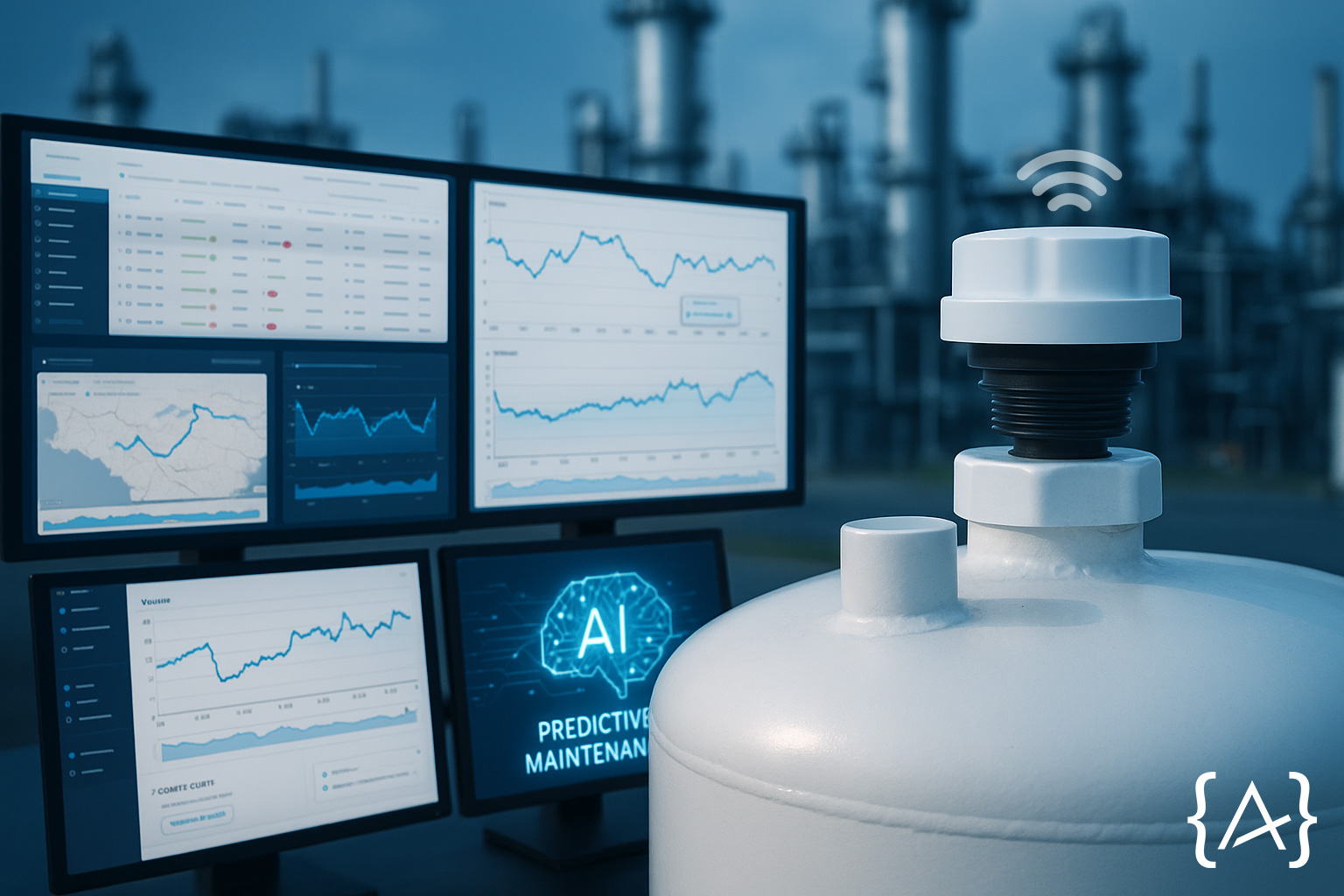
In a constantly changing industrial world, unplanned equipment downtime represents a major risk to business performance and profitability. Faced with these challenges, the predictive maintenance is emerging as a strategic solution for better anticipating failuresextend the asset lifespanand optimize intervention management.
At the crossroads of IoT technologiestechnologiesdata analysis andartificial intelligencethis approach is transforming the way manufacturers monitor thecondition of their machines. By identifying weak signals of wear and tear or malfunction, predictive maintenance enables you to take action. at the right timeneither too early (as in preventive action) nor too late (as in corrective action).
Understanding predictive maintenance
A simple, accessible definition
The predictive maintenance is a method for managing industrial equipment based onanalysis of data from sensors to anticipate failures before they cause a production stoppage.
Instead of replacing a part based on time or duty cycle, this approach relies on theactual of theasset monitored. This triggers a intervention only when necessary, neither too early nor too late.
👉 Think of maintenance as a medical check-up for your machines. Where preventive maintenance prescribes check-ups every six months, predictive maintenance works like a connected watch that constantly monitors your health, and alerts you to any unusual signs.
Why is it crucial to Industry 4.0?
In a connected and automated industry, every downtime can lead to a loss of loss of critical loss of critical performance productionor even a breakdown in the supply chain.
The predictive maintenance makes it possible to exploit the wealth of data collected in real time to optimize asset managementreduce costs and improve overall system overall system reliability.
It is fully in line with the logic ofindustry 4.0where objects are interconnected, processes automated, and the decision-making data-assisted decision-making.
Differences with preventive and condition-based maintenance
It is common to confuse maintenance approaches, especially between preventive and predictive predictive. Yet they are based on different logics.
Criteria | Preventive | Conditional | Predictive |
---|---|---|---|
Based on… | Production time or cycle | Observable state (visual, auditory) | Automatic data analysis |
Tools | Fixed planning | Simple sensors | Sensors + artificial intelligence |
Frequency | Planned (fixed) | Depends on spot checks | Depends on real-time data evolution |
Objective | Reduce known faults | React to visible signs | Anticipate invisible failures |
How predictive maintenance works
Regular data collection and monitoring
At the heart of predictive maintenance lies the fundamental principle of continuous monitoring of equipment condition. Thanks to intelligent sensorsattached to industrial machinesit is possible to capture continuous data physical data (temperature, vibration, pressure, current, etc.) that reflect their actual operating status.
These information is then transmitted via suitable networks (NB-IoT, LTE-M, LPWAN( LoRa /Sigfox) …) to a centralized platform platform, where it is stored, historized and ready for analyzed.
🛠️ Expert advice
The sensors to use vary according to the context:
- Vibrations Pumps, rotary motors
- Temperature / humidity : food processing environments
- Pressure / flow : hydraulic systems
- Current / voltage Electrical equipment
Choosing the right sensors means targeting critical critical parts and capture reliable indicators for decision-making.
Analysis via artificial intelligence and machine learning
Once the collectedthey are processed by predictive predictive models based onartificial intelligence (AI) and machine learning. These technologies can detect anomalies invisible to the naked eye or difficult to perceive with conventional tools.
In concrete terms, the system “learns” the normal behavior of an industrial asset and identifies significant deviations in the data, the precursor of an impending imminent failure.
💡 Example of a model used a recurrent neural network (RNN) can predict an abnormal deviation in a motor’s temperature from its operating history.
Extending equipment service life
Well-maintained equipment longeroperates more efficiently and requires fewer unscheduled replacements. Thanks to rigorous monitoring ofparts statusand wear thresholds, manufacturers can optimize their return on equipment return on equipment investment.
Take the example of an industrial pump: without maintenance, its service life can be limited to 4 years. With regular checks and targeted replacements, it can reach 7 to 9 years with no loss of performance.
📊 Key figures (average) :
- +40% longer life for condition-monitored motors
- +60% on bearings serviced every 6 months
- 25% less energy consumption with a well-tuned compressor
🛠️ Expert advice
“Plan controls according to criticality equipment, and not simply according to its age. This is the the right balance between cost and performance..”
Automating maintenance decisions
Analysis alone is not enough: to be useful, predictive predictive maintenance must be translated into concrete actions. That’s why the most advanced systems allow you toautomate the decision or generate a prioritized alert based on the level of risk level.
📥 Example if a pump shows an abnormal increase in vibrationAn alert is sent to the maintenance manager via the CMMS. A task is automatically created to check the bearing wearwith a link to analysis data.
This approach limits unnecessary interventions while avoiding unscheduled downtimeoptimizing both intervention time and maintenance maintenance costs.
Key technologies and tools
IoT sensors and collection platforms
The sensor is the entry point for predictive maintenance. It transformsactual condition of equipment at digital data exploitable. It must be accurate, robust and adapted to the industrial environment in which it is deployed.
Here are the most commonly used sensors:
- Vibration sensors for monitoring motors, pumps or bearings
- Temperature sensors useful for detecting overheating components
- Current and voltage sensors to evaluate power consumption or identify drifts
- Pressure and flow sensors essential in hydraulic hydraulic or or pneumatic circuits
- Level sensors widely used in silos or tanks (e.g. food or fuel)
These sensors then communicate with an IoT platform platform centralize, visualizethen transmit data to analysis tools.
📋 Checklist – Getting started with reliable data collection
- Choose sensors adapted to the industrial environment
- Check sampling frequency according to the type of fault to be detected
- Provide reliable network connectivity (LoRaLPWAN, NB-IoT, LTE-M…)
- Guaranteeing an energy supply (long-life battery, mains supply, etc.)
- Ensure data compatibility with the analysis platform
Artificial intelligence and machine learning
The raw data from sensors are only of value once they have been interpreted. This is where artificial intelligence (AI) comes into play. Thanks to machine learningthe platform learns the normal behaviors of a systemthen detects anomalies likely to precede a failure.
For example, models can :
- Identify progressive wear of a motor by a variation in vibratory signature
- Predicting electrical failure from a change in consumption
- Anticipate clogging on a filter by analyzing differential pressure
This dynamic analysis makes it possible to switch from a control logic to an intelligent prediction logic. intelligent prediction.
CMMS and integration tools
To make predictive maintenance operationalit must be connected to thesoftware ecosystem software ecosystem, in particular the CMMS (Computerized Maintenance Management System).
The essential functions of a compatible CMMS are :
- Automated scheduling interventions
- Traceability of operations and equipment history
- Prioritization of tasks according to criticality level
- Real-time notifications predictive alerts
- Consolidated dashboards integrating sensor data
🔌 Please note
A open API is essential for to communicate effectively with IoT platforms. It guarantees fluidity between systems, without manual re-entry or loss of information.
What we offer at Four Data
At Four Datawe have designed an industrial IoT platform fully modular and agnosticable to integrate any type of type of sensorsensor machine or network.
Our solution allows you to :
- Collect data in real time via a variety of sensors
- View the status of your equipment at any time
- Set up intelligent alerts based on automatic analysis
- Easily connect your existing infrastructure (CMMS, ERP, BI, etc.)
We can also help you choose the right network connectivity best suited to your industrial environment, thanks to our proven technologies (NB-IoT, LTE-M, LoRa, Sigfox…).
🚀 Key benefit
Our platform adapts to all industrial environments, even the most isolated. To help you choose the most appropriate connectivity (Sigfox RCZ1 in Europe, LoRa or LTE-M in France, Swisscom in Switzerland…), we provide an online tool that lets you test network coverage at your location in real time:
👉 Test your LoRa, Sigfox or LPWAN coverage
Strategic advantages for the industry
Reduced downtime
One of the most immediate benefits of predictive maintenance is the significant reduction in breakdowns and unplanned downtimewhich are often costly and destabilizing for thecompany.
Here are the observable impacts:
- ✅ Fewer production interruptions production thanks to targeted interventions
- ✅ Anticipation of critical faults before they result in a complete shutdown
- ✅ Better availability of industrial industrial assets
- ✅ Less stress and pressure for maintenance teams
📊 Key figures
On average, our industrial customers see a 25% to 30% reduction in unplanned downtime after implementing a predictive maintenance strategy.
Optimizing operating costs
Beyond shutdowns over-maintenance costly. Replacing parts in perfect condition or intervene too frequently generates unnecessary costs. unnecessary costs. By acting only when necessary, predictive maintenance improves resource allocation.
👷♂️ Mini-cas A food industry player detects, via Four Data, a progressive temperature drift on a cold chain motor. Result:
- Scheduled intervention during the day, avoiding emergency repairs
- Savings: ~€1,200, simply by avoiding a call-out + loss of products.
🧩 Practical tip
Give priority to critical equipmentwhose failure would have a direct impact have a direct impact on industrial performance or safety safety. This is where the return on investment is the fastest.
Extending equipment service life
Monitor theactual of machines allows action to be taken before wear becomes irreversible. By keeping components in their optimum operating range, the equipment of equipment is extended.
Better operations planning
By making potential potential riskspredictive maintenance makes it possible to integrate interventions into production scheduleavoiding last-minute disruptions.
The benefits in the field are tangible:
- ✅ Fewer unforeseen events in the workshops
- ✅ Less pressure on technical teams
- ✅ Better coordination between maintenance and production
- ✅ Reducing stocks of emergency spare parts
📘 Expert advice
Integrate alerts from your predictive system into your planning tools (CMMS, ERP, etc.). This enables you to transform a technical risk at controlled logistics actionwithout disrupting the organization.
Deploying a predictive maintenance strategy
🧾 Initial audit and selection of data to be monitored
The success of a predictive maintenance project depends first and foremost on an in-depth in-depth diagnosis. This stage identifies critical machinesthe key data to be collectedand operational objectives.
📋 Start-up checklist :
- Identify strategic industrial assets (costly, sensitive, complex)
- List types of data required: vibration, temperature, intensity, pressure, etc.
- Check availability availability of compatible or existing sensors
- Evaluate collection frequency (continuous, periodic)
- Define the targeted use cases (prevention of a recurring defect, process improvement, securing an asset, etc.).
⚠️ Point of vigilance
A good project starts with a clear clear framing What type of failure do we want to prevent? On which machine? What is the logic behind performance or cost ? This step determines everything else.
Choice of networks and protocols (NB-IoT, LTE-M…)
Once the sensors have been defined, the choice of communication network that will link your equipment to the processing platform. This choice depends on the site topologysite data volume and constraints in terms ofenergy autonomy.
Comparison of the main IoT networks :
Network | Range | Data rate | Sensor autonomy | Ideal environment |
---|---|---|---|---|
LoRa /Sigfox |
Long | Low | Excellent | Large sites, isolated buildings |
NB-IoT | Medium to long | Medium | Very good | Urban / semi-urban areas |
LTE-M | Medium | High | Good | Mobile sites, throughput requirements |
Wi-Fi | Short | High | Medium | Sites equipped with infrastructure |
📡 Did you know?
Thanks to the modularity of networks such as LoRa or NB-IoTa project can start with a small small pilot area before being extended on a large scalewithout changing the architecture.
Setting up a POC, followed by full-scale deployment
Before generalizing a predictive maintenance solution, it is advisable to go through a Proof of Concept (POC)i.e. a full-scale test on a limited perimeter.
✅ Key steps :
- Define a concrete use case (e.g. detecting wear on a critical motor)
- Select equipment and install sensors
- Configure data collection and analysis models
- Measuring results : alert reliability, time saved, costs avoided
- Adapt and industrialize deployment to other machines or sites
This process makes it possible to technical and economic validation the solution before extending it.
🌟 Key benefit
With Four Data, you benefit from a single single point of contact with expertise the complete chain sensors, connectivity, platform, integration with your tools.
👉 This guarantees a coherent fast and scalable.
Four Data support every step of the way
At Four Datawe have put in place a proven proven methodology to accompany you from the initial need to the industrialization of your IoT and predictive maintenance project:
🔧 Our 5-step approach :
- Understanding of your field constraints and industrial challenges
- Ideation Definition of scope, objectives and type of sensors
- POC installation and testing on site or in real-life conditions
- Deployment solution scaling
- Monitoring: continuous optimization and enhancement of collected data
🌟 Key benefit
With Four Data, you benefit from a single single point of contact with expertise the complete chain sensors, connectivity, platform, integration with your tools.
👉 This guarantees a coherent fast and scalable.
Limits and challenges to anticipate
If predictive predictive maintenance offers many advantages, its implementation also raises technical technical, human and organizational challenges. Anticipating them increases the project’s chances of success.
System complexity
Risks :
- Heterogeneous industrial architecture, with different generations of equipment
- Difficulty in standardizing data from multiple sources
- Incompatibilities between sensors, software and communication protocols
Recommendations:
- Start with a controllable perimeterFocus on one or two critical items of equipment
- Choose open open, interoperable IoT solutions
- Rely on a partner capable of managing both hardware and data
Initial cost and expected ROI
Risks :
- Initial investment (sensors, network, platform) sometimes considered high
- Doubts about short-term profitability, especially in the absence of historical data
- Underestimation of maintenance costs for the system itself
Recommendations:
- Prioritize assets with a high impact on production costs
- Measuring gains right from the POC : downtime avoided, parts preserved, interventions anticipated
- Integrate indirect savings: fewer breakdowns, less operational stress
👥 Acceptance by field teams
Risks :
- Resistance to change, fear of technology or automation
- Feeling of excessive surveillance
- Lack of training on tools or alert interpretation
Recommendations:
- Involve technicians right from the test phase
- Show concrete concrete benefits saving time, reducing emergencies
- Plan short, field-oriented training sessions
Data security and governance
Risks :
- Exposure of sensitive data (production plans, performance levels)
- Compliance issues (RGPD, network security)
- Poor lifecycle management of collected data
Recommendations:
- Ensure that the platform complies with cybersecurity standards
- Host data in secure, sovereign environments and sovereign environments
- Define a clear data retention and usage policy
🧠 Myth vs. reality
Myth Predictive maintenance is reserved for large industrial companies with substantial resources.
Reality Thanks to modular IoT solutionssolutions degressive sensor costsand the possibility of phased deployment, it is now accessible accessible to any industrial structureincluding SMEs.
Future prospects
AI-powered automated predictive maintenance
The future of predictive maintenance lies in a dynamic ofintelligent automation. Visit artificial intelligence models become capable of not only predict failuresbut also automatically recommend the best best corrective action to undertake, or even to carry it outwithout human intervention in certain cases.
Industrial companies are moving towards self-learning self-learning systemsThis continuous adaptation capability will enable us to move from simple detection to more sophisticated detection. This capacity for continuous adaptation will enable us to move from simple detection to more effective autonomous decision-makingreinforcing resilience of production lines.
Connectivity enhanced by IoT
The massive deployment of connected sensorscoupled with the development of 5G, LTE-M and NB-IoTnetworks, opens the way to real-time predictive maintenanceeven in difficult or remote environments.
Thanks to increased bandwidth and reduced reduced latencydata can be retrieved and analyzed more quickly, improving system system responsiveness. In particular, this development will make it possible to integrate mobile objects (industrial vehicles, site equipment, etc.) in continuous monitoring logics.
Towards intelligent industrial platforms
Tomorrow’s platforms will go far beyond maintenance. They will become decision kernelsintegrating production data, maintenance, quality, energy and even environment to orchestrate all industrial operations.
These ecosystems combine IoT, AI and analytics will enable companies to manage the overall performance of their plant in real time, with personalized interfaces, dynamic dynamic dashboardsand contextualized predictive models.
📈 Key figures
The global predictive maintenance market is expected to reach 45.5 billion dollars by 2030according to several projections, driven by the rise of smart manufacturing and connected technologies.
FAQ – Frequently asked questions about preventive maintenance
Make data a lever for industrial performance
The predictive maintenance is no longer a concept of the future, but a reality attainable reality to all industrial companies, whatever their size. By exploiting data from your equipment, you can transform your interventions into real levers for performance performance, savings and reliability.
👉 Would you like to launch your predictive maintenance project?
Our teams at Four Data are with you every step of the way, from sensor to platform, from testing to large-scale deployment.
📞 Contact an expert now for a diagnosis tailored to your industrial environment.
You may also be interested in these articles :